Forklifts play a vital role in warehouses and distribution centres across the UK, enabling the efficient movement of heavy loads and streamlining logistics operations. However, their widespread use in a busy warehouse environment also presents significant safety challenges. Forklift accidents remain a leading cause of workplace injuries, property damage, and operational disruptions.
From collisions and tip-overs to pedestrian accidents, the risks associated with forklift operations can have serious consequences, including severe injuries and even fatalities. According to the Health and Safety Executive (HSE), improper forklift use is a major contributor to workplace accidents in industrial settings. These incidents put workers at risk and result in costly downtime, legal liabilities, and reputational damage for businesses.
Implementing effective forklift safety strategies is essential for maintaining a secure working environment. By prioritising effective training, adherence to safety regulations and integration of safety technologies alongside the implantation of forklift and pedestrian segregation practices and regular equipment maintenance, warehouse operators can significantly reduce the likelihood of accidents. This article explores proven safety measures that help mitigate risks and ensure forklift operations remain efficient and safe in warehouse and distribution settings.
How SSoW & Continuous Improvement Prevent Forklift Accidents
Establishing a structured and proactive approach to forklift safety is crucial in reducing workplace accidents. A combination of Safe Systems of Work (SSoW), continuous improvement, and regular safety inspections ensures that businesses maintain high safety standards while minimising operational risks.
Best Practice Approaches in Safe Systems of Work and Risk Assessment
A Safe System of Work (SSoW) provides a structured framework to identify, control, and mitigate hazards associated with forklift operations. Implementing best practices in SSoW includes:
- Comprehensive Risk Assessments: Conducting thorough risk assessments to identify hazards such as narrow aisles, blind spots, and high pedestrian traffic. Employers must ensure compliance with the Health and Safety at Work Act 1974 and HSE guidance.
- Standard Operating Procedures (SOPs): Clearly defined SOPs should be established, covering aspects like speed limits, designated travel routes, and pedestrian zones.
- Training and Competency Requirements: Ensuring that only trained and certified forklift operators are permitted to use the equipment. Regular refresher training should be mandatory.
- Use of Signage and Traffic Management: Implementing clear signage, floor markings, and barriers to separate forklifts from pedestrians.
Emergency Preparedness: Developing and communicating emergency procedures to ensure quick response in case of accidents.
By integrating these best practices, businesses can create a structured, safer working environment that significantly reduces the likelihood of forklift-related accidents.
How Continuous Improvement Supports Workplace Safety Objectives
Continuous improvement is an essential component of an effective forklift safety programme. By regularly evaluating and refining safety protocols, businesses can enhance workplace safety and reduce incident rates. Key aspects include:
- Incident Reporting and Learning from Near Misses: Encouraging workers to report near-misses and minor incidents allows organisations to address potential hazards before they result in serious accidents.
- Regular Safety Audits and Reviews: Conducting routine safety audits helps identify gaps in safety procedures and areas for improvement.
- Employee Feedback and Engagement: Actively involving workers in safety discussions and decision-making fosters a safety-first culture.
- Technology Integration: Implementing safety innovations such as proximity sensors, speed controls, and automated alerts can enhance safety awareness and monitoring.
- Ongoing Training and Development: As industry standards evolve, continuous training ensures employees stay updated on the latest safety practices.
By embedding continuous improvement into workplace culture, businesses can systematically enhance their safety measures and maintain a proactive approach to accident prevention.
Importance of Regular Safety Inspections and Risk Reduction Strategies
Routine safety inspections are a fundamental aspect of forklift accident prevention. Regular checks help identify equipment defects, unsafe practices, and environmental hazards before they lead to accidents.
- Pre-Use and Daily Checks: Operators should carry out daily pre-use inspections, checking brakes, lights, steering, and tyres to ensure the forklift is safe to operate.
- Scheduled Maintenance: Preventative maintenance, in line with manufacturer recommendations, reduces the risk of mechanical failures.
- Environmental Safety Inspections: Regular assessments of warehouse layouts, floor conditions, and lighting help eliminate potential hazards.
- Compliance with Legal Standards: Adhering to LOLER (Lifting Operations and Lifting Equipment Regulations) and PUWER (Provision and Use of Work Equipment Regulations) ensures that forklifts are legally compliant and fit for use.
- Risk Reduction Strategies: Implementing collision-avoidance technologies, speed-limiting devices, and enhanced operator visibility solutions can significantly reduce accidents.
- Physical or Virtual Segregation: Installing barriers, segregated walkways, and/or virtual protection building zones helps to keep workers and vehicles apart.
By prioritising safety inspections and risk reduction strategies, businesses can maintain a safe operational environment while minimising costly disruptions.
Common Hazards for Forklift Operators
Forklift operations in warehouses, distribution centres, depots, and yards present various safety challenges. Accidents often occur due to a combination of operator error, environmental hazards, and equipment issues. Understanding these common hazards is crucial in implementing effective safety solutions.
Key accident causes include:
- Collisions with Pedestrians or Objects: Poor visibility, lack of designated walkways, and driver distraction can result in serious accidents involving pedestrians, inventory, or racking systems.
- Tip-Overs and Overturning: Excessive speed, driving with unstable or raised loads, or operating on uneven surfaces, ramps, or inclines can cause forklifts to tip over, leading to injuries and damage to goods.
- Load Handling Errors: Exceeding the forklifts’ SWL (Safe Working Load) parameters, overloading, incorrect stacking, and unstable loads increase the risk of falling objects and damage to goods.
- Mechanical Failures: Inadequate maintenance and overlooked pre-use checks can lead to brake failures, damaged or worn lift chains, steering malfunctions, operating with bent or damaged forks, or hydraulic issues such as oil leaks.
- Blind Spots and Restricted Visibility: Operators may struggle with poor visibility due to warehouse layout, inadequate lighting, high shelving, or carrying oversized phloads, increasing the risk of collisions.
- Unsafe Driving Practices: Speeding, abrupt turns, driving with a raised load, or failure to follow designated travel routes can lead to loss of control and workplace accidents.
- Fatigue and Lack of Training: Tired or poorly trained operators are more likely to make errors, compromising safety for themselves and others.
By recognising these hazards, businesses can implement targeted safety measures to prevent forklift-related incidents. The next section will explore practical solutions to mitigate these risks effectively.
How To Prevent Forklift Accidents In The Workplace
Preventing forklift accidents requires a combination of proactive safety measures, advanced technology, and strict adherence to workplace safety protocols. By integrating modern safety solutions alongside comprehensive training and risk assessments, businesses can significantly reduce the likelihood of forklift-related incidents.
Key strategies for accident prevention include:
- Implementing physical safety features such as barriers and pedestrian route floor markings.
- Implementing collision avoidance systems to detect and prevent potential crashes.
- Enforcing speed control measures to ensure forklifts operate at safe speeds.
- Using visual alert systems such as warning lights to improve visibility and awareness.
- Deploying proximity warning systems to detect hazards and protect pedestrians.
- Maintaining regular training and inspections to uphold safety standards.
Below, we explore these key solutions in more detail.
Active Collision Avoidance Systems
Active Collision Avoidance Systems (ACAS) play a critical role in preventing forklift accidents by detecting obstacles and alerting operators before a collision occurs. These systems use advanced sensors and real-time monitoring to automatically intervene if a risk is detected, significantly reducing the chance of accidents in busy warehouse environments. By installing ACAS, businesses can:
- Reduce the risk of forklift collisions.
- Enhance operator awareness of blind spots and restricted areas.
- Minimise damage to racking, goods, and infrastructure.
Learn more about Transmon Active Collision Avoidance Systems (ACAS).
Speed Control Systems
Speeding is a major cause of forklift accidents, particularly in high-traffic areas. Speed Control Systems help mitigate this risk by limiting forklift speeds based on location, load weight, and operational conditions. These systems ensure that operators maintain safe speeds, reducing the likelihood of rollovers, collisions, and tip-overs. Benefits of speed control include:
- Increased safety in pedestrian-heavy areas.
- Prevention of sudden stops and sharp turns that can cause accidents.
- Compliance with workplace speed regulations.
Discover more about our Speed Control Systems.
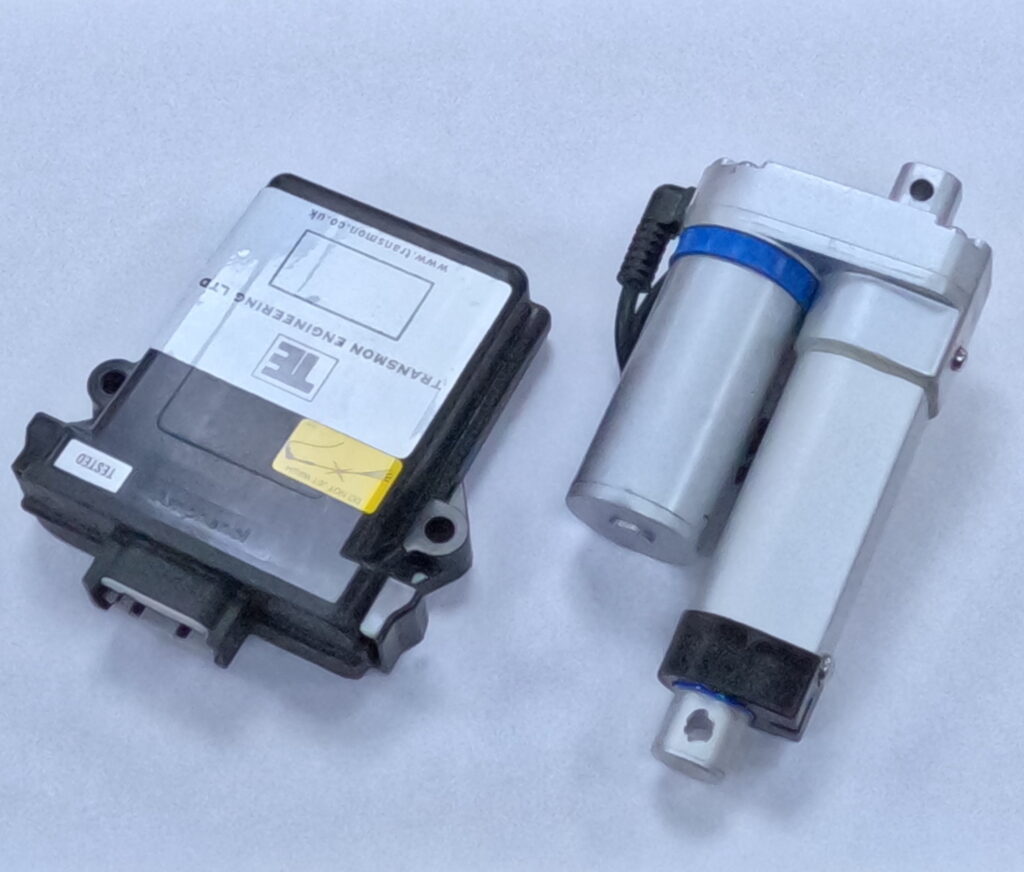
The Transmon RSPC2 forklift speed control system.
Forklift Cameras
Forklift Camera Systems enhance operator visibility by reducing blind spots and providing a clearer view of the surroundings. These systems are particularly useful in high-shelving or pallet warehouses and areas with limited visibility, helping to prevent collisions and improve load-handling precision. Key benefits of Forklift Cameras include:
- Increased visibility in hard-to-see areas, reducing the risk of blind spot accidents.
- Improved accuracy when handling and positioning loads into storage locations.
- Enhanced operator confidence, leading to safer and more efficient operations.
Discover our range of Forklift Cameras.
Warning Lights
Warning lights are a simple yet highly effective visual alert system for forklift operators and pedestrians. These lights improve awareness by illuminating the forklift’s movement path, helping to prevent accidents in areas with limited visibility. By integrating warning lights, businesses can:
- Increase visibility in poorly lit environments.
- Alert nearby workers and other forklift operators of approaching vehicles.
- Reduce the risk of collisions at intersections and blind spots.
Find out more about Warning Lights from Transmon.
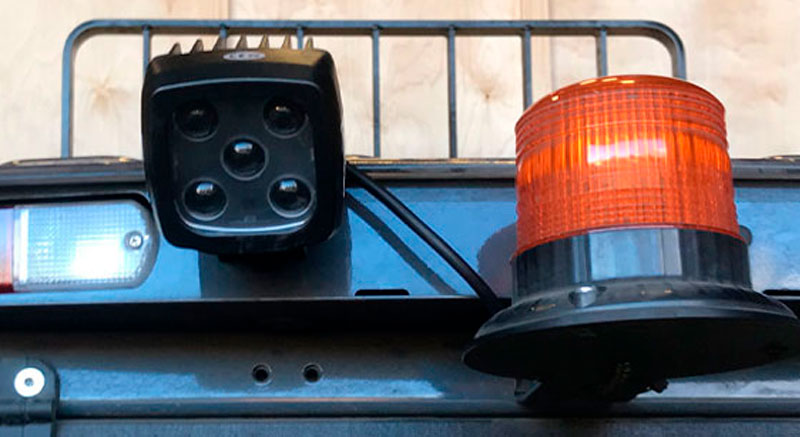
Increase site safety with Forklift Warning Lights.
Proximity Warning Systems
Proximity Warning Systems are essential for preventing forklift accidents by alerting operators to nearby hazards, including pedestrians, inventory, other vehicles, and building infrastructure. These systems use RFID or sensor-based technology to monitor the forklift’s surroundings, providing real-time alerts when a potential collision is detected. By integrating Proximity Warning Systems, operators can:
- Improve pedestrian safety in warehouses and distribution centres.
- Reduce forklift-related injuries and near-misses.
- Enhance operator awareness and reaction times to avoid accidents.
Explore our Proximity Warning Systems.
Summary: A Holistic Approach to Forklift Safety
By combining Transmon’s cutting-edge safety solutions alongside detailed risk assessments, continuous improvement programmes, and adherence to safety regulations and best practices, businesses can adopt a comprehensive, multi-layered approach to forklift accident prevention. Each system covered in this article – Active Collision Avoidance, Speed Control, Cameras, Warning Lights, and Proximity Warning Systems – is designed to mitigate risks, improve visibility, and enhance overall workplace safety.
Implementing these solutions not only protects workers and reduces accident-related costs but also ensures that warehouses and distribution centres operate efficiently and in compliance with UK safety regulations. Investing in forklift safety is not just a legal obligation, it’s a long-term commitment to establishing a safer and more productive work environment.
To find out how our products can improve site safety and reduce the risk of forklift accidents, contact one of our experts today by calling 0116 260 4200.