The industrial landscape remains as competitive as ever where efficient warehouse operations are critical to maintaining a company’s profitability and customer satisfaction. At the very heart of these operations lies the fleet of forklifts and material handling equipment that are integral to keeping goods on the move and productivity at an all-time high. However, the cost of owning, operating, and maintaining a fleet of forklift trucks can quickly escalate, impacting operational efficiency and profitability if not carefully managed.
Effective fleet management is about more than just cost savings; it’s a strategy for improving operational efficiency, reducing downtime and unplanned maintenance, and extending the lifespan of your valuable equipment. Whether your fleet comprises a handful of forklifts or a large-scale operation with diverse material handling machinery, controlling costs while optimising performance is essential for long-term success.
In our latest blog, we look at five practical ways to reduce fleet costs and improve efficiency, helping businesses achieve the right balance between performance, safety, and costs. From implementing preventive maintenance programs to leveraging collision avoidance technology, these strategies can offer robust and easy-to-deploy solutions to enhance operations while staying budget-conscious.
We will be covering the following fleet cost reduction strategies in this article:
- Control Speed, Control Costs
- Reduce Engine Idle Time
- Prevent Engine Damage & Wear
- Track & Monitor Fleet Usage
- Prevent & Reduce Collisions & Impact Damage
Fleet Cost Challenges in Warehouse Operations
Managing a forklift and machinery fleet comes with several cost challenges that can quickly add up if not closely monitored and addressed swiftly. Excessive fuel usage is a common issue, often driven by inefficient driving habits or extended idling, which leads to higher operating costs. External forces can also play a part, such as cost rises in domestic fuel & labour, and the impact of trade wars and global uncertainty on operational pricing. Equipment damage, whether from collisions, poor maintenance, misuse or overuse, can result in unforeseen and expensive repairs and costly downtime. Damage to stock and building infrastructure can also add significant costs to the business and operational impact as a result of collisions by forklift trucks.
Additionally, inefficient working practices and operator behaviour, such as improper handling or failure to follow best practices, can exacerbate wear and tear, further increasing maintenance costs and reducing overall fleet efficiency. Identifying and addressing these challenges is essential for controlling expenses and optimising fleet performance.
The choice of forklift power units also impacts the overall cost of operations. Lithium-ion (Li-ion) and lead-acid batteries are two primary power sources for forklifts and have differing benefits. Lead-acid batteries are a more cost-effective option with proven reliability, yet they require regular maintenance and have a slower charging time. In contrast, Li-ion batteries offer faster charging, longer lifespans, and are maintenance-free, making them ideal for high-demand operations. They also allow opportunity charging during short breaks, increasing productivity. While Li-ion batteries have a higher upfront cost, their efficiency and reduced downtime often result in significant long-term savings.
Solutions To Help Reduce Fleet Costs & Improve Efficiency
For both UK and global fleet operators striving to optimise material handling operations, reducing their operational costs and improving overall efficiency are critical objectives. Transmon Engineering offers a wide range of innovative systems and solutions designed to address the common challenges faced by operators of forklift and machinery fleets. Whether it’s excessive fuel usage, equipment wear, or inefficient operator behaviour, Transmon’s advanced technologies, including speed limiters, idle timeout systems, engine monitoring systems, fleet management tools, and impact detection solutions, provide comprehensive strategies to enhance safety and performance.
By integrating these systems into your operations, Transmon Engineering enables customers to achieve measurable savings, extend the lifespan of equipment, and create a safer, more productive workplace. With a focus on tailored solutions and reliable integration, Transmon Engineering is your partner of choice in maintaining a smarter, safer, and more cost-effective fleet.
1. Control Speed, Control Costs
One vital yet often overlooked component of fleet management is the impact of forklift speed on operating costs. Excessive speed can lead to higher fuel consumption, increased equipment wear & tear, and an increased risk of accidents or damage to goods. Controlling forklift speed is not just a safety measure, it’s a cost-saving strategy that can extend the life of your equipment, protect your inventory, and reduce overall operational expenditure.
The Role of Speed Limiters
Speed limiters are integrated devices designed to regulate the maximum speed of forklift trucks, ensuring operators adhere to predetermined limits. These speed limiter devices provide significant benefits, including:
- Reduced Fuel Usage – LPG and diesel-powered forklifts operating at excessive speeds will typically consume more fuel. By capping the speed, speed limiters promote smoother acceleration and deceleration whilst reducing wheel spin and excessive engine RPMs which can lead to measurable savings in fuel costs. Over time, these savings can substantially impact your fleet’s operating budget.
- Minimised Equipment Wear – High-speed operation accelerates wear and tear on critical components such as tyres, brakes, and transmissions. Speed limiters reduce the stress placed on these parts, helping to lower maintenance and replacement costs. For example, smoother operation at controlled speeds can extend the life of tyres and reduce the frequency of repairs to brakes and other key components.
- Improved Safety and Reduced Damage – Beyond cost savings, controlling forklift speed also contributes to workplace safety by minimising the risk of collisions or accidents. This, in turn, reduces the likelihood of equipment or product damage, lowering repair and replacement expenses.
Implementing Speed Controls
Many modern forklifts may come equipped with built-in speed control systems, while older models can easily be retrofitted with integrated speed limiters. It’s also beneficial to pair speed limiters with operator training programs, ensuring employees understand the importance of adhering to speed limits for both safety and cost efficiency. Skilled drivers especially those who are made accountable for their driving habits, typically operate forklift trucks more safely and efficiently. This leads to enhanced usage of the trucks and reduces the risk of potential damage to the forklifts through excessive speed.
By leveraging speed limiters and enforcing speed regulations, businesses can achieve safer and more cost-effective operations while preserving the performance and longevity of their material handling equipment.
2. Reduce Engine Idle Time
Engine idling is all too common across warehouses, distribution centres, and depot environments. However, engine idling is a significantly costly issue in forklift operations, leading to unnecessary fuel consumption, energy waste, and increased wear and tear on the engine. Forklifts left idling for extended periods not only burn through fuel, but also accumulate engine hours, which can shorten the lifespan of critical components and adversely inflate maintenance costs.
To address this, many modern forklifts are equipped with idle timeout systems, which automatically shut down the engine and turn off the ignition protecting the starter battery from over-discharge after a predetermined period of inactivity. These systems offer multiple advantages:
- Lower Fuel and Power Usage – By preventing forklifts from idling unnecessarily, idle timeout systems significantly reduce fuel consumption in internal combustion forklifts and power usage in electric models. This leads to direct cost savings and supports environmental sustainability efforts by lowering emissions.
- Engine Protection – Excessive idling can cause heat build-up and inefficient burning of fuel in internal combustion engines, leading to premature wear. For electric forklifts, idling can drain battery power, reducing the forklift’s runtime and increasing its charging frequency. Idle timeout systems are designed to minimise these issues, helping to extend the overall life of the engine or battery.
- Enhanced Operator Awareness – Idle timeout systems can also encourage operators to adopt more efficient driving habits, such as turning off forklifts during breaks or periods of inactivity. Combined with comprehensive training and monitoring programs, this can lead to a cultural shift toward more mindful equipment usage which directly and positively impacts productivity and operational costs.
By reducing engine idling using integrated idle timeout technology, businesses can lower operating costs, protect their fleet, and promote sustainable practices, ensuring their material handling operations remain efficient and cost-effective.
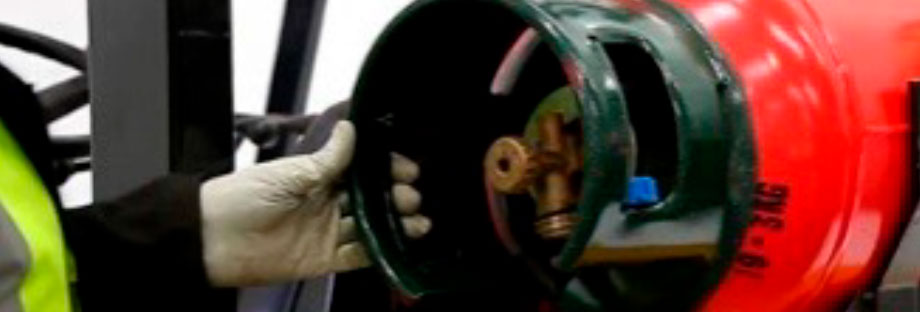
The TE Power Saver Idle Timeout system reduces fuel or power usage and protects the engine by automatically shutting down an idle forklift truck.
3. Prevent Engine Damage & Wear
Maintaining the health of forklift engines is critical to minimising downtime and avoiding costly repairs. Without proper oversight of the fleet’s health status, issues such as overheating, oil pressure drops, or irregular engine operation can go unnoticed until significant damage occurs. Engine monitoring systems provide a proactive solution, helping to prevent damage and extend the lifespan of your equipment.
How Engine Monitoring Systems Work
Engine monitoring systems track key performance indicators such as coolant temperature, oil pressure, RPMs, and operating hours in real-time. When these metrics exceed the agreed, safe thresholds, the system alerts operators or automatically takes protective actions, such as reducing engine power or shutting it down automatically.
Benefits of Engine Monitoring Systems
- Early Problem Detection – By continuously monitoring your overall fleet health and engine performance, these systems identify potential issues before they escalate into serious damage, such as detecting low oil pressure early to prevent the engine from seizing up which would incur costly repairs.
- Reduced Wear and Tear – Fleet health monitoring systems ensure engines operate within their optimal parameters, reducing the strain caused by overheating, over-revving, or running with insufficient lubrication. This proactive approach helps to minimise the wear and tear of the engine, thereby extending its operational life.
- Cost Savings on Repairs – Preventive measures enabled by monitoring systems reduce the likelihood of major breakdowns, which often require extensive and expensive repairs. By addressing small issues early, businesses can avoid unplanned downtime and maintain a consistent level of operations.
- Improved Maintenance Scheduling – These systems provide valuable data that fleet managers can use to optimize maintenance schedules. Knowing exactly when components need attention ensures that forklifts are serviced efficiently, avoiding both premature servicing and neglect.
By investing in engine monitoring systems, businesses can safeguard their forklifts against damage, minimise repair costs, and maintain a reliable, efficient fleet. This technology not only protects equipment but also supports long-term fleet cost control and operational resilience.
4. Track & Monitor Fleet Usage
To effectively manage a fleet of forklifts and material handling equipment, operators need visibility on how each asset is used on a daily basis. Fleet management systems (FMS) provide a centralised platform for tracking and monitoring the usage of forklifts, allowing businesses to make data-driven decisions that reduce operational costs and improve efficiency.
How Fleet Management Systems Work
Fleet management systems use telematics to collect real-time data from forklifts, including metrics such as operating hours, travel hours, idle times, and maintenance needs. This data is then analysed in-depth and presented through intuitive dashboards, offering actionable insights for optimising fleet operations.
Benefits of Fleet Management Systems
- Optimised Equipment Utilisation – FMS enables businesses to identify equipment or assets that are either underutilised or overworked. By redistributing tasks or adjusting the size of fleet, companies can ensure optimal usage of resources, reducing unnecessary equipment wear and extending the lifespan.
- Reduced Fuel and Energy Costs – By monitoring fuel consumption, idle time, and operator behaviour, fleet management systems help pinpoint areas where there are inefficiencies. Addressing these issues, such as reducing engine idling or improving route planning, leads to measurable cost savings on fuel or energy.
- Streamlined Maintenance – FMS tracks usage metrics like engine hours and provides alerts to managers when equipment is due for maintenance. This ensures timely servicing, preventing costly breakdowns while avoiding unnecessary maintenance on low-usage equipment.
- Enhanced Operator Productivity – With fully integrated real-time tracking, fleet managers can effectively monitor operator performance, identify any inefficiencies, and provide targeted training to improve the performance and productivity of forklift drivers. This creates a more skilled and effective workforce and reduces time lost to the improper use of equipment.
- Data-Driven Decision Making – The data collected by FMS offers insights into fleet performance trends. This helps businesses develop positive strategies and make informed decisions about the effectiveness of their fleet, before taking the appropriate actions across equipment replacement, procurement, or downsizing to further reduce costs.
By leveraging innovative fleet management systems, businesses can gain a comprehensive view of their operations, reduce waste, and enhance overall efficiency. This technology not only helps lower operational costs but also ensures a more sustainable and productive material handling environment.
5. Prevent & Reduce Collisions & Impact Damage
Collisions and impact damage are among the most common causes of costly repairs in forklift operations. Accidents not only lead to equipment damage but can also harm personnel, disrupt workflows, and result in product losses or damage to building infrastructure. Impact detection systems offer a proactive solution to enhance safety, monitor driver behaviour, and minimise the cost of repairs.
How Impact Detection Systems Work
Impact detection systems are equipped with sensors that register collisions or abnormal impacts on forklifts. These systems log who, what & when details such as the time, location, and severity of the event. Some advanced systems can also alert supervisors in real-time, enabling swift corrective action.
Benefits of Impact Detection Systems
- Enhanced Safety – By monitoring and recording impacts, these systems promote safer operation. When drivers are aware that their actions are being monitored, they tend to adopt more careful driving habits, reducing the likelihood of accidents.
- Minimised Repair Costs – Collisions in and around a warehouse or depot environment can result in costly damage to forklifts, racking, or stored goods. Impact detection systems help identify the precise cause of accidents, allowing corrective action to be taken to prevent any recurrence. Additionally, early detection of minor impacts can prevent further damage that might escalate into expensive repairs.
- Improved Accountability – Impact logs provide a clear record of incidents, creating a culture of accountability. Managers can use this data to address specific operator issues or implement additional or more in-depth training programs tailored to improve safety and reduce risks.
- Lower Insurance and Liability Costs – Reduced accident rates can lead to lower insurance premiums and fewer liability claims. Documentation provided by impact detection systems can also serve as valuable evidence in case of disputes or insurance claims.
- Prolonged Equipment Life – By reducing the frequency and severity of impacts, these systems help prevent wear and tear on forklifts and associated infrastructure, extending the life of valuable assets and lowering total cost of ownership.
Integrating impact detection systems into fleet operations not only enhances workplace safety but also delivers substantial cost savings by minimising the cost of repairs and fostering a proactive approach to risk management.
Implementing Your Fleet Cost Reduction Strategy
Efficient fleet management is crucial for reducing costs and maintaining high-performance operations. From controlling forklift speed and reducing idle timeouts to implementing engine monitoring, fleet management, and impact detection systems, these strategies address common cost challenges such as excessive fuel consumption, equipment damage, and inefficient operator behaviour.
Transmon Engineering specialises in designing and integrating a wide range of advanced systems, offering industry-leading, tailored solutions that optimise fleet performance and deliver the balance between safety and productivity. With a proven track record of enhancing efficiency and reducing operational costs, Transmon can help your business achieve a safer, more cost-effective material handling environment.
Contact our team today to start your journey. Speak to our friendly team by calling 0116 260 4200.